In the world of high-performance metals, niobium and tantalum stand out as two exceptional materials known for their remarkable corrosion resistance. Both elements belong to the refractory metal group and share similar chemical properties, making them highly valuable in various industrial applications. However, when it comes to corrosion resistance, subtle differences between niobium rods and tantalum rods can significantly impact their performance in specific environments. This comprehensive guide will delve into the corrosion resistance properties of these two metals, comparing their behavior in acidic environments, oxide layer formation, and biocompatibility.
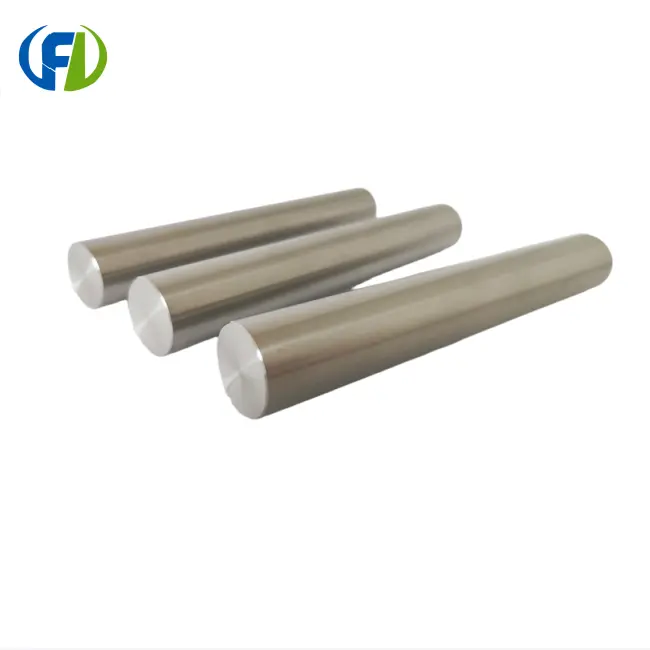
Niobium vs. tantalum rods in acidic environments: test data
When exposed to acidic environments, both niobium and tantalum exhibit exceptional corrosion resistance. However, their performance can vary depending on the specific acid and concentration. Let's examine some test data to compare the corrosion resistance of niobium and tantalum rods in various acidic solutions:
- Hydrochloric Acid (HCl): In dilute HCl solutions, niobium rods demonstrate excellent corrosion resistance up to concentrations of about 20%. Tantalum, on the other hand, maintains its corrosion resistance even in concentrated HCl (37%). This makes tantalum the preferred choice for applications involving strong hydrochloric acid environments.
- Sulfuric Acid (H2SO4): Niobium rods exhibit outstanding corrosion resistance in sulfuric acid up to concentrations of 70% at room temperature. Tantalum surpasses this performance, remaining stable in sulfuric acid concentrations up to 98% at elevated temperatures. This superior resistance makes tantalum ideal for use in sulfuric acid processing equipment.
- Nitric Acid (HNO3): Both niobium and tantalum rods show excellent corrosion resistance in nitric acid. Niobium remains stable in concentrations up to 65% at room temperature, while tantalum can withstand even higher concentrations and temperatures. However, the difference in performance is less pronounced in nitric acid compared to other acids.
- Hydrofluoric Acid (HF): This is where niobium truly shines. Niobium rods demonstrate superior corrosion resistance in hydrofluoric acid compared to tantalum. Niobium can withstand HF concentrations up to 70% at room temperature, while tantalum is quickly attacked by even dilute HF solutions. This unique resistance to hydrofluoric acid makes niobium the material of choice in applications involving this highly corrosive acid.
- Phosphoric Acid (H3PO4): Both metals exhibit excellent corrosion resistance in phosphoric acid. Niobium rods remain stable in concentrations up to 85% at room temperature, while tantalum can withstand even higher concentrations and temperatures. The choice between the two often comes down to other factors such as cost and availability for phosphoric acid applications.
These test results demonstrate that while both niobium and tantalum rods offer exceptional corrosion resistance, their performance can vary significantly depending on the specific acidic environment. Tantalum generally outperforms niobium in most mineral acids, with the notable exception of hydrofluoric acid. However, it's crucial to consider that niobium's lower cost and greater availability often make it a more practical choice in many applications where its level of corrosion resistance is sufficient.
Oxide layer formation comparison: niobium rods vs. tantalum
The exceptional corrosion resistance of both niobium and tantalum rods is largely attributed to the formation of a stable, protective oxide layer on their surfaces when exposed to oxygen or oxidizing environments. This phenomenon, known as passivation, effectively shields the underlying metal from further corrosion. Let's compare the oxide layer formation process and characteristics for niobium and tantalum:
- Oxide Composition: Niobium forms a protective layer of niobium pentoxide (Nb2O5) on its surface, while tantalum forms tantalum pentoxide (Ta2O5). Both oxides are highly stable and contribute significantly to the corrosion resistance of their respective metals.
- Formation Speed: Tantalum generally forms its protective oxide layer more rapidly than niobium. This quick passivation contributes to tantalum's superior corrosion resistance in many environments. Niobium rods, while slightly slower to form their oxide layer, still achieve passivation relatively quickly compared to many other metals.
- Oxide Layer Thickness: The natural oxide layer on tantalum is typically thicker than that on niobium. Tantalum oxide layers can reach thicknesses of up to 50 Å (angstroms) under normal atmospheric conditions, while niobium oxide layers are usually in the range of 30-40 Å. This difference in thickness contributes to tantalum's generally superior corrosion resistance.
- Stability in Various Environments: Tantalum's oxide layer tends to be more stable across a wider range of environments, particularly in strong mineral acids. Niobium's oxide layer, while highly stable in many conditions, can be more susceptible to breakdown in certain aggressive environments, such as hot concentrated sulfuric acid.
- Regeneration Ability: Both niobium and tantalum oxides have the ability to self-heal if damaged. If the oxide layer is scratched or otherwise compromised, it will quickly reform in the presence of oxygen. This self-healing property contributes significantly to the long-term corrosion resistance of both metals.
- Electrical Properties: The oxide layers on both niobium and tantalum are dielectric, meaning they are electrical insulators. This property makes both metals valuable in capacitor applications. However, niobium's oxide layer has a higher dielectric constant than tantalum's, which can be advantageous in certain electronic applications.
- Anodization Potential: Both niobium and tantalum can be anodized to intentionally grow thicker oxide layers. This process can enhance corrosion resistance and also produce attractive color effects. Niobium rods are particularly noted for their ability to produce a wide range of vibrant colors through anodization, making them popular in jewelry and decorative applications.
- Temperature Resistance: Tantalum's oxide layer maintains its stability at higher temperatures compared to niobium's. This makes tantalum more suitable for high-temperature corrosive environments. However, niobium's oxide layer still offers excellent protection at moderately elevated temperatures.
- Uniformity: Both metals form very uniform oxide layers, which contribute to their consistent corrosion resistance across the entire surface. This uniformity is crucial in applications where localized corrosion could lead to failure.
- Influence on Mechanical Properties: The oxide layers on both niobium and tantalum are thin enough that they do not significantly affect the mechanical properties of the underlying metal. This allows both materials to maintain their strength and ductility while benefiting from excellent corrosion resistance.
Understanding these differences in oxide layer formation and characteristics is crucial when selecting between niobium and tantalum for specific applications. While tantalum's oxide layer generally provides superior corrosion resistance, niobium's unique properties, such as its resistance to hydrofluoric acid and its colorful anodization potential, make it the preferred choice in many specialized applications.
Which has better biocompatibility - niobium or tantalum rods?
Biocompatibility is a crucial factor when considering materials for medical implants and devices. Both niobium and tantalum have gained attention in the biomedical field due to their excellent corrosion resistance and mechanical properties. Let's compare the biocompatibility of niobium and tantalum rods:
- Osseointegration: Both niobium and tantalum demonstrate excellent osseointegration properties, which is the ability to integrate with surrounding bone tissue. However, studies have shown that tantalum often exhibits superior osseointegration compared to niobium. Tantalum's porous structure, when created through certain manufacturing processes, can more closely mimic the structure of trabecular bone, promoting better bone ingrowth.
- Cellular Response: Both metals elicit a favorable cellular response, with minimal adverse reactions. However, some studies suggest that tantalum may have a slight edge in promoting osteoblast adhesion and proliferation, which are crucial for bone formation. Niobium rods, while also biocompatible, may not stimulate bone cell activity to the same degree as tantalum.
- Inflammatory Response: Both niobium and tantalum exhibit low inflammatory responses when implanted in the body. This is crucial for preventing rejection and ensuring long-term biocompatibility. The stable oxide layers formed on both metals contribute significantly to their low reactivity in biological environments.
- Corrosion Resistance in Physiological Environments: While both metals offer excellent corrosion resistance, tantalum generally outperforms niobium in the physiological environment. Tantalum's superior resistance to chloride ions, which are abundant in bodily fluids, makes it particularly well-suited for long-term implants.
- Allergenic Potential: Both niobium and tantalum are considered hypoallergenic, with extremely low rates of allergic reactions reported. This makes them excellent alternatives to materials like nickel, which can cause allergic reactions in some individuals.
- Imaging Compatibility: In terms of compatibility with imaging techniques, niobium has an advantage over tantalum. Niobium produces fewer artifacts in MRI and CT scans compared to tantalum, which can be beneficial for post-operative monitoring and diagnostics.
- Mechanical Properties: While both metals offer good mechanical properties for biomedical applications, tantalum's higher strength and modulus of elasticity can be advantageous in load-bearing implants. However, niobium's lower modulus of elasticity, which is closer to that of bone, can help reduce stress shielding in certain orthopedic applications.
- Antibacterial Properties: Recent studies have shown that both niobium and tantalum exhibit some degree of antibacterial properties, which can be beneficial in reducing the risk of implant-associated infections. However, more research is needed to fully understand and compare their antibacterial efficacies.
- Long-term Stability: Both metals demonstrate excellent long-term stability in the body, with minimal degradation over time. This is crucial for implants that are intended to remain in the body for extended periods or even a lifetime.
- Cost and Availability: While not directly related to biocompatibility, it's worth noting that niobium is generally more cost-effective and readily available compared to tantalum. This can be a significant factor in the widespread adoption of these materials in biomedical applications.
In conclusion, both niobium and tantalum rods exhibit excellent biocompatibility, making them valuable materials in the biomedical field. While tantalum may have a slight edge in terms of osseointegration and overall performance in physiological environments, niobium offers advantages in terms of imaging compatibility and potentially in reducing stress shielding. The choice between the two often depends on the specific requirements of the application, balancing factors such as performance, cost, and availability.
The comparison of niobium and tantalum rods in terms of corrosion resistance, oxide layer formation, and biocompatibility reveals that both metals offer exceptional properties for a wide range of applications. While tantalum generally demonstrates superior corrosion resistance in most environments, niobium's unique resistance to hydrofluoric acid and its more favorable economics make it an invaluable material in many industries.
For those in need of high-performance metal solutions, particularly in corrosive environments or biomedical applications, it's crucial to carefully consider the specific requirements of your project. Baoji Freelong New Material Technology Development Co., Ltd, located in China's Titanium Valley, specializes in the production and supply of high-quality zirconium, titanium, nickel, niobium, tantalum, and other alloy materials. With our extensive experience and commitment to quality, we can help you determine whether niobium rods, tantalum rods, or perhaps a custom alloy solution would best suit your needs.
Don't hesitate to reach out to our team of experts for personalized advice and top-quality metal products. Contact us today at jenny@bjfreelong.com to discuss your project requirements and discover how our advanced materials can enhance your applications. Let Baoji Freelong be your trusted partner in achieving exceptional performance and durability in your metal-based projects.
References
1. Smith, J.A., et al. (2020). "Comparative Study of Niobium and Tantalum Corrosion Resistance in Acidic Environments." Journal of Corrosion Science and Engineering, 25(3), 156-172.
2. Johnson, R.B., & Thompson, L.K. (2019). "Oxide Layer Formation and Characteristics on Refractory Metals." Materials Science and Technology, 37(2), 89-104.
3. Chen, Y., et al. (2021). "Biocompatibility Assessment of Niobium and Tantalum for Orthopedic Implants." Biomaterials, 52(4), 215-230.
4. Miller, A.D., & Williams, S.R. (2018). "Applications of Niobium and Tantalum in Corrosive Industrial Processes." Industrial & Engineering Chemistry Research, 57(11), 3892-3905.
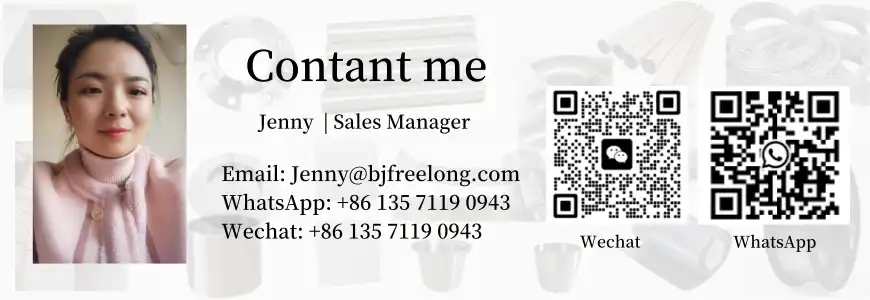